Glass Making Hot Glass Workshop in Istanbul
135,00 €
Description
Duration: 2 hours
Location: Galata – Taksim / ISTANBUL
Lesson Teachings: Available in English and Turkish
Cost : 135 Euro per person
Overview ;
Welcome to our Art Studio. In our art center, we teach private and group workshops for Adults and children. Our times are flexible soo upon your request, we can teach you techniques using our tools and materials. In the end of this workshop, you will have a fnished art piece that you can take with you. We teach the following masterclasses ;
- Fusion Glass – Hot Glass Making
- Glass Shaping with Fire
- Glass Shaping with Molding Technique
- Glass Mosaics Workshop
- Glass Painting Workshop
- Jewellery Making with Glass
What is Included
- In our lessons; we can teach beginner & advanced level Professional Artists
- Turkish Ottoman or Modern Style Hot Glass Making
- All equipment for needed for the Glass workshop
- In the end of the workshop you will have a finished piece of art work.
- Workshop Area, Aprons & Gloves
- Turkish Tea & Water
Meeting Point ;
Here is our Art Studio Address ;
Google Maps : https://goo.gl/maps/uXuyRmELZsx
Events of Istanbul – Les Arts Turcs Art Studio
Alemdar Mh. Incili Cavus St.
No: 19 Floor : 3 (Behind The Underground Cistern)
Sultanahmet 34110
Istanbul, Turkey
Contact : Phone or Whatsapp : +90 544 220 10 22
E-mail : info@eventsofistanbul.com
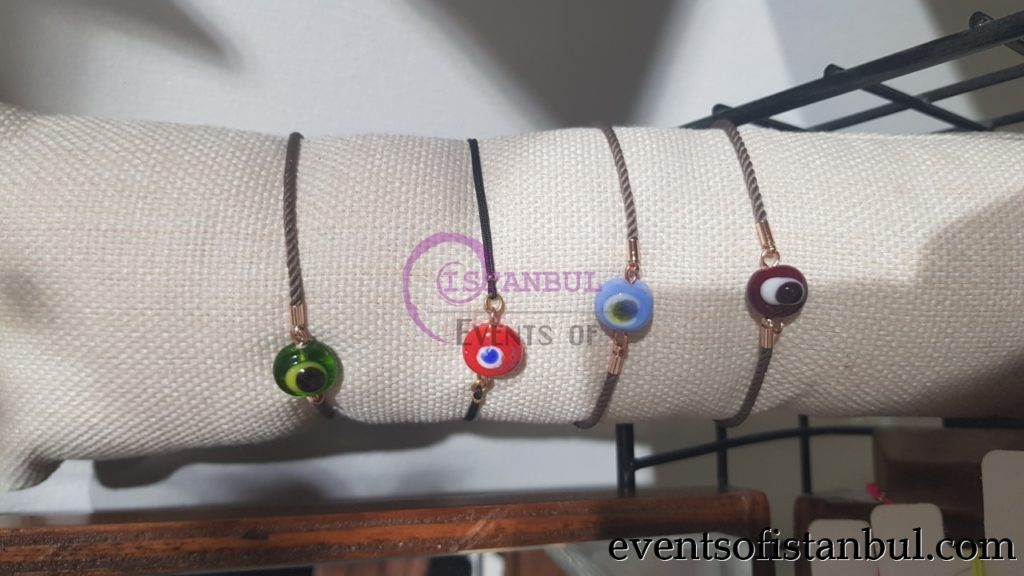
Additional Information ;
Glass Fusion Workshop
The world of colored glass …
We cut colorful glasses, cut and project them together, and bake them in high-grade ovens… The result is excellent jewelry, plates decorated …
Flame Shaping Workshop
The magical world of hot glass is like therapy.
The blue of the flame and the charm of the colors go beyond the work done.
Sometimes… turns into beads and jewelry …
Sometimes there is a handful of happiness …
Molding Workshop,
In this workshop you will get the basics of your journey in creating glass works. A perfect journey through the mud and molds towards the Glass awaits you.
If you don’t have glass art dreams, “NOT for you”
Metal Clay Workshop
You will shape the metals that have been shaped hand like dough and create the jewelry and objects of your dreams hand.
Metal master? forget it.
You will be able to shape the metal yourself.
Glass Painting Workshop
You will learn the intricacies of creating wonders with special glass paints and painting techniques.
We will teach you the basics. You will be the limits of your design and creativity.
Pate de Verre Workshop
It is a little more than the glass molding technique, a little similar …
The most valuable method of blending glasses into powder and paste and forming mixtures of different colors. It works perfectly after.
Stained Glass Workshop
Let’s learn the basics of this art, which we can briefly call glass painting.
Let’s start with simple techniques and studies and move towards complex and perfect works. Whether your works are gifted or prepared for your exhibition.
Glass Mine Workshop
We make enamel …
So we cover the surface of the metals with glass.
It is up to you to show the construction techniques and firing details and to create unique works from us. Whether you buy, earn money or give it as a gift, add it to your collection ..
Painting workshop
We carry out this workshop, in which we will introduce the basics of watercolor painting, only for groups in the spaces determined you.
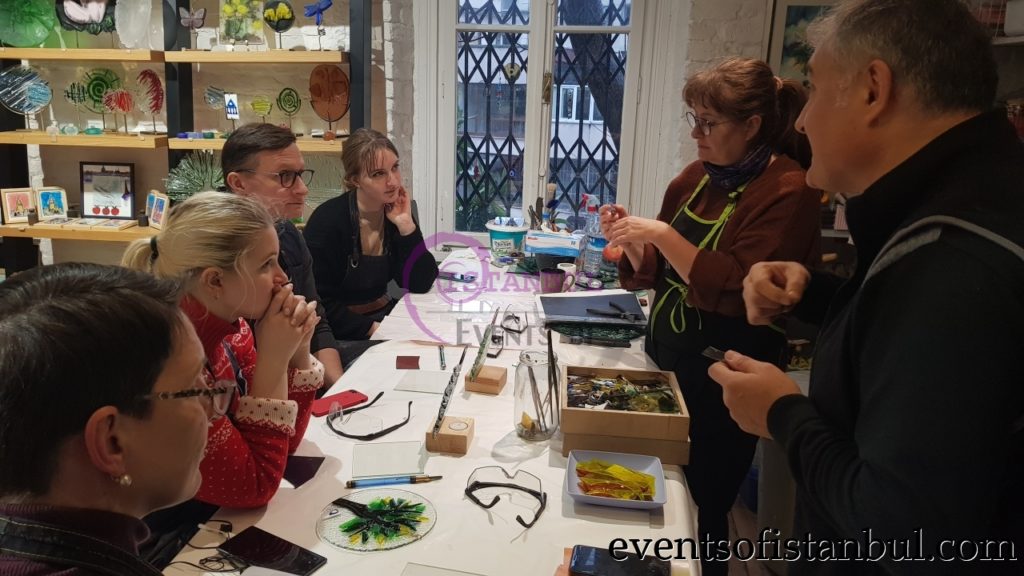
Ancient Glass of Asia Minor
Glass-making Techniques and Other Glass Terms
Virtually all the techniques of glass-making in use today were known in antiquity. The tools have not changed essentially since the discovery of glass-blowing, although on technical level furnaces, chemistry and mass-production methods have been improved. Most of the advances in glass manufacture are the result of the industrial revolution; mechanical pressing, acid-etching and sand-blasting are techniques that have evolved only in the last two hundred years.
Core-forming
the earliest method of making glass vessels is known as core-forming. Small containers were produced trailing molten glass over a shaped, clay core fashioned on the end of a metal rod. Upon completion, the rod was removed, the vessel annealed (gradually cooled), and the clay core scraped out. The Erimtan Collection contains only one example of a core-formed vessel. It represents one of the last types made using the technique.
Casting
This process involved the shaping of molten glass in a closed mould or over an open former. The earliest use of casting is found in the production of mosaic glass vessels during the Late Bronze Age. They were made fusing together thin slices of coloured glass made from canes. In the Iron Age, when translucent monochrome or colourless glass became popular, a simpler method was used for making open-shaped vessels, wherethe hot glass was sagged over a former. Closed vessels, on the other hand, were probably cast using the lost-wax technique. A mould was made creating a wax or wax-coated model of the object to be produced. The model was enveloped in clay or plaster and then baked, so that the wax melted, leaving a mould into which molten or, more probably, powdered glass could be poured. After casting, the vessels were allowed to cool, and then they were usually cut and ground into their final form.
Blowing
the discovery of glass-blowing occurred slightly before the middle of the first century BC in the Syro-Palestinian region of the Near East. It was, however, not until the use of a hollow metal blow-pipe became accepted practice (probably in the last quarter of the first century BC) that the invention was fully appreciated. The combination of the blow-pipe and the knowledge of inflation revolutionised the glass industry, enabling craftsmen to make vessels more quickly, at less expense and in a greater variety of shapes.
Mould-blowing
This technique developed from the invention of glass-blowing, probably in the first quarter of the first century AD. It allowed the glass-maker to replicate designs and shapes at will, using a pre-made clay, metal or wooden mould.
Pattern-moulding
This was a method in which a gather of glass was partially formed in a mould. The pattern thus created was then expanded and usually spiral-twisted during the re-inflation of the vessel.
Tralling
The application of glass threads, often in a contrasting colour, gave added interest to free-blown glass vessels.
Cutting
Cutting as a type of decoration was a separate operation carried out when the vessel was cold. The Romans distinguished clearly between the glass- maker and the glass-cutter, the former being called a vitrearius and the latter a diatretarius. While the glass-blower was principally involved in the manipulation of hot glass, the glass-cutter employed skills that were more closely related to those of the gem-cutter.
Fire-polishing
The re-introduction of a vessel into the furnace in order to soften and thus smooth out any irregularities on the surface of the glass.
Marvering
Rolling softened glass over a flat surface, usually in order to smooth an added trail decoration into the side of the vessel.
Pontil
A metal rod that enabled the glass-maker to hold and manipulate an object while working on it. After blowing, the pontil was attached to the bottom of a vessel while the rim, handle(s) and other decorative elements were added. The pontil often left a scar or mark where it had been attached to the vessel. Not all vessels, however, have a pontil mark. This may be because the glass-maker had taken the trouble to remove the scar grinding and polishing the finished article. Alternatively, the vessel may have been held a clamp or pair of pincers, instead at the end of a pontil. Many small perfume bottles show signs of such tooling around the neck, indicating that for mass-produced, cheap items this was the preferred way of holding a vessel.
Kick
A depression in the bottom of a vessel, usually caused pressure exerted in the application of the pontil.
Weathering
The iridescence now visible on many ancient glasses is not original or intentional but the result of weathering. Over time the composition of glass can deteriorate, creating a chemical deposit that often flakes off to leave a pitted and iridescent surface. This not only obscures the original colour and transparency of the glass but can also destroy the decorative details and, in extreme cases, the vessel itself. Not all ancient glass, however, is weathered. The weathering is caused contact with certain types of soil, moisture and even frequent changes in temperature and humidity.
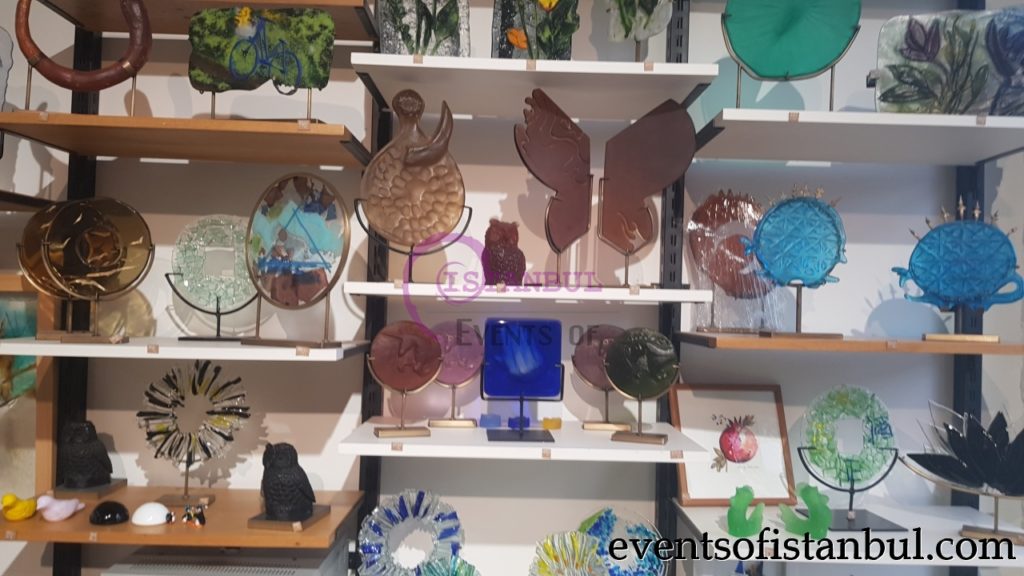